CH Power Tools
Client
CH Power Tools
Services
PHP DevelopmentSoftware DevelopmentLaravel DevelopmentAPIs & Integrations
Discipline
Tool Repair & Inventory Management
Location
UK
CH Power Tools came to us with a challenge. They weren’t looking for just another inventory management system; they needed a custom tool management solution built entirely around the way they worked.
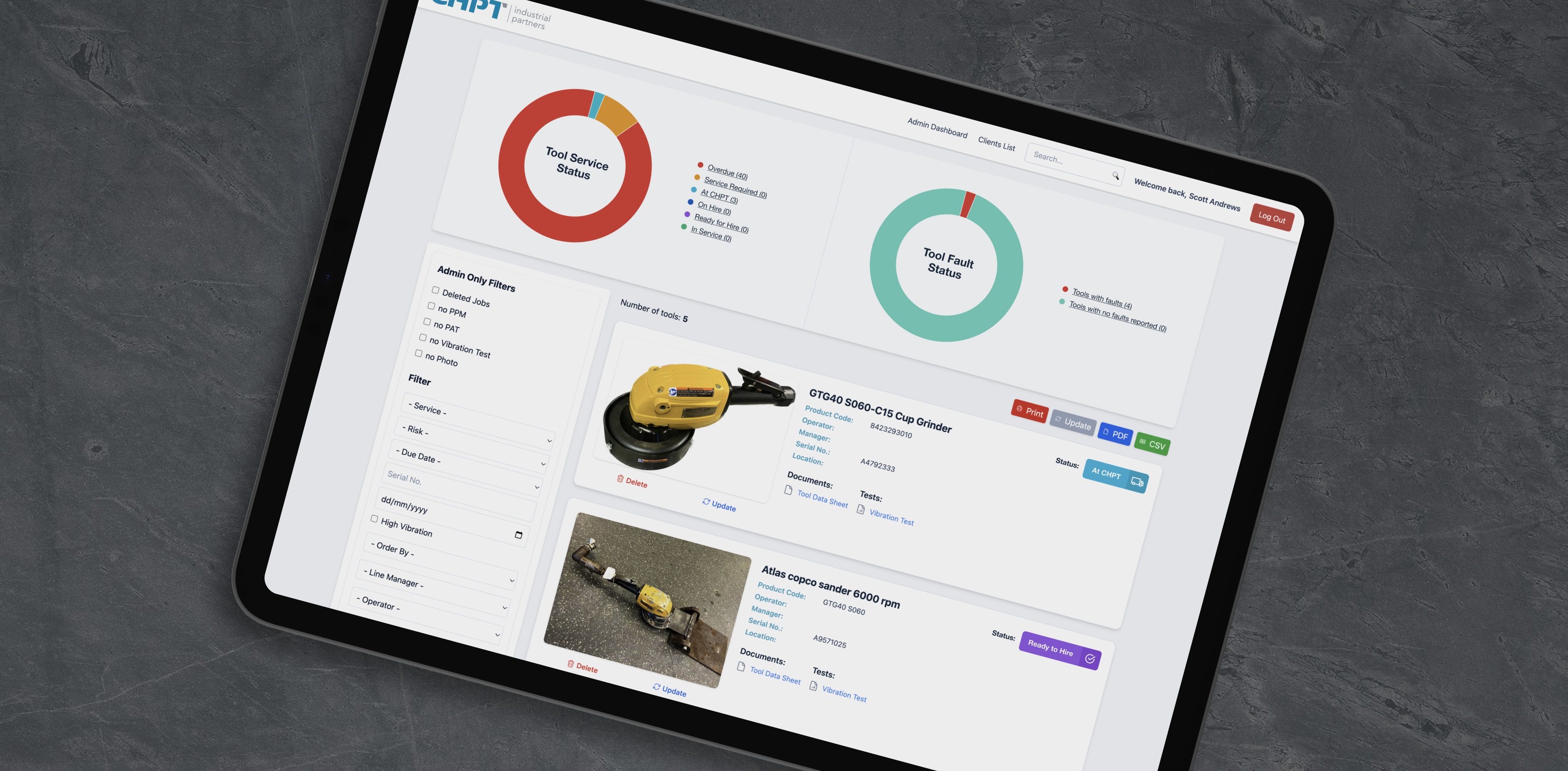
CH Power Tools came to us with a challenge. They weren’t looking for just another inventory management system; they needed a custom tool management solution built entirely around the way they worked.
The Challenge
A Unique set of Requirements, Demands a Unique Solution
CH Power Tools supports small to large organisations by repairing, servicing, and managing thousands of tools, often handling inventories of upwards of 4,000 individual tools.
CH Power Tools were growing, winning more contracts and supporting much larger companies. This increased the pressure on their existing management processes, which were manual and hands-on. This presented a challenge when trying to scale, which was holding them back.
What was needed was more thana basic inventory system. CH Power Tools needed a system that could track each tool in real time, not just by customer, but by location, operator, and maintenance status. Managers needed visibility across entire teams. Servicing schedules had to be tracked and flagged automatically. And when tools were damaged or faulty, CH Power Tools needed a way to be instantly notified and begin the collection process.
No off-the-shelf product could provide a solution. So together, we built a customer solution from scratch.
The Solution
A Custom Tool Management System Built for CH Power Tools
We worked closely with CH Power Tools, visiting their offices, working alongside their different teams to help us understand every detail of how they operate and what each area of the business needed from the system. What we delivered was a tailored, end-to-end tool management system that’s still at the core of their business today.
The system allows for each tool to be assigned to a work bay or an individual operator. Operators themselves are grouped under managers, allowing for layered oversight. From the dashboard, CH Power Tools and the customer can see instantly where every tool is, who’s responsible for it and its status.
When a tool is due for servicing or a vibration test, the system doesn’t wait for someone to check; it flags it. The dashboard highlights tools that are:
- Currently being serviced at CH Power Tools
- Due for service in the coming month
- Already overdue
If a tool is damaged or faulty, the operator simply marks it in the system. CH Power Tools are notified, a collection is scheduled, and the tool’s status is updated. As the tool progresses through the repair process, the status is updated from "awaiting collection" to "at CH Power Tools" to "on its way back."
Every tool has a profile, product code, serial no, location, status, manager, operator, and documentation such as datasheets and vibration test records. Nothing is lost, nothing is unclear.
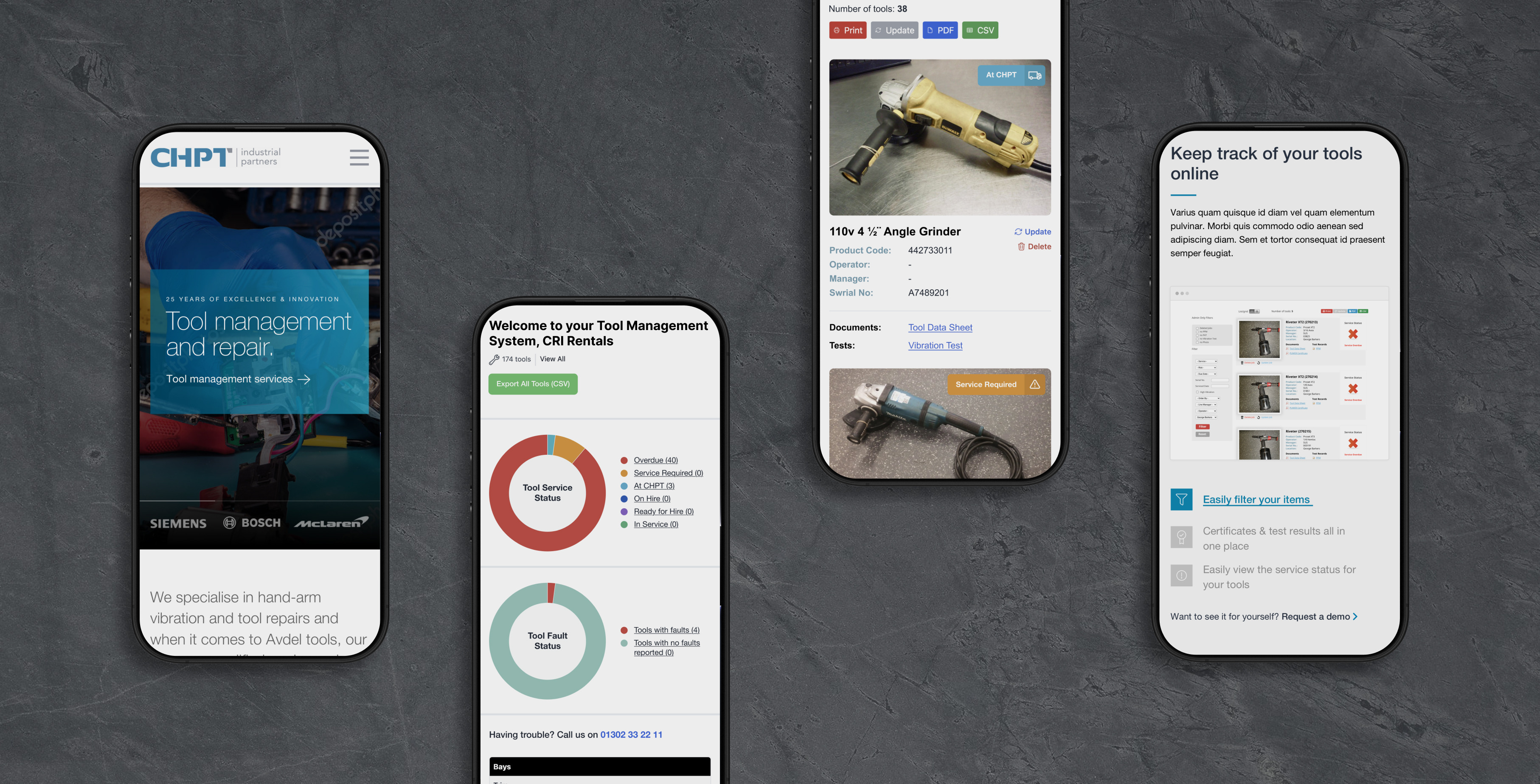
The Result
A Long-Term Solution, Not Just a System
Today, the CH Power Tools tool management system sits at the centre of their business. It’s helped them reduce tool loss, improve service scheduling, and streamline communications between their teams and clients.
Most importantly, it’s a system that has allowed them to grow. What started as a complex request has evolved into a long-term partnership, and more than a decade later, we’re still proud to be the team behind it.
More services related to CH Power Tools
We create custom software designed to drive meaningful transformations and growth for your business.
Software DevelopmentWe design and build bespoke applications and e-commerce systems that can make a real difference to businesses.
Laravel DevelopmentFrom booking engines to logistic management, we build secure, scalable solutions to grow with your business.
APIs & IntegrationsSeamless Connectivity. We specialise in integrating your systems with third-party APIs to streamline operations, enhance functionality and improve user experience.
View All ServicesOther Work
Here are some more case studies that you might find relevant. Due to client sensivity we cannot always show the full detail of a project. If any of the work seems relevant to what you need, feel free to give us a call.